Sheet metal processing
Sheet metal working is a broad term that refers to a variety of processes used to shape and process sheet metal into finished products. These processes are important in the manufacturing industry and are used to create everything from car bodies and aircraft parts to household appliances and building components.
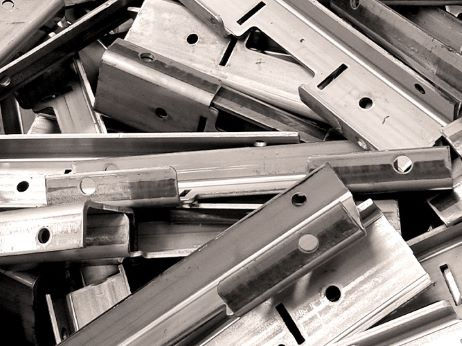
Common Processes in sheet metal processing
Cutting:
A process where the sheet metal is cut to the desired size and shape using mechanical or hydraulic cutting tools. This includes punching and laser cutting.
Punching: A punching press is used to punch holes in or cut out shapes from sheet metal.
Laser cutting: A laser beam is used to cut the sheet with high precision.
Bending:
A process where sheet metal is bent to a specific angle or shape. This can be done using press brakes or bending machines.
Edge pressing: The plate is placed between a punch and a pad and is bent to the desired angle when the punch is pressed down.
Roll bending: The sheet is passed through a series of rollers to create a curved or cylindrical shape.
Deep drawing:
A process where the sheet is formed into a hollow shape by being drawn into a mold with a punch. This is often used to create complex three-dimensional shapes such as car bodies and kitchen sinks.
Punching and embossing:
Processes where the sheet is formed by pressing it against a mold or pad to create patterns, textures or holes.
Embossing: Creates raised or recessed patterns in the sheet metal.
Punching: Cutting or punching out specific shapes from the sheet metal.
Welding:
Joins two or more sheet metal parts by melting and joining the material. MIG, TIG and laser welding are common welding methods for sheet metal.
Rolling:
A process in which the sheet is passed through rollers to reduce its thickness or to create long, flat sheets.
Cold rolling: Processing the sheet at room temperature to improve surface quality and maintain dimensional accuracy.
Hot rolling: Processing of sheet metal at high temperatures to form thicker and larger parts.
Material being processed
Steel:
Often used in the construction and automotive industries for its strength and durability.
Stainless steel:
Popular in the food, medical and chemical industries for its corrosion resistance.
Aluminum:
Used in the aerospace industry and for lightweight components due to its light weight and good strength.
Copper and brass:
Used in electrical and decorative applications for their conductivity and aesthetic appearance.
Areas of use
Automotive industry:
Manufacture of bodies, chassis parts and engine mounts.
The construction industry:
Creation of roof panels, ventilation systems and structural components.
Aviation industry:
Production of fuselages, wings and other important structural parts.
White goods:
Manufacture of housings and parts for refrigerators, stoves and dishwashers.
Electronics:
Creation of chassis and casings for computers, mobile phones and other electronic devices.
Advantages of sheet metal processing
Versatility:
The ability to create complex shapes and detailed components.
Efficiency:
High production speeds and the possibility of automation make it cost-effective for large volumes.
Precision:
Advanced technologies such as laser cutting and CNC control provide high precision and accuracy.
Material utilization:
Effective use of materials with minimal waste, which is both economical and environmentally friendly.